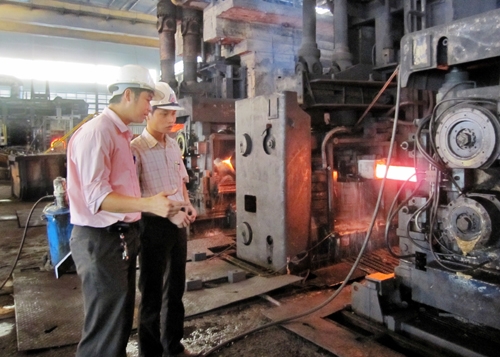
Trong quá trình lao động sản xuất, thời gian qua các kỹ sư trẻ của Nhà máy Cán thép Thái Nguyên (thuộc Công ty Cổ phần Gang thép Thái Nguyên) đã có nhiều đề tài khoa học có hiệu quả thiết thực. Các anh đã góp phần duy trì ổn định hoạt động của hệ thống máy móc thiết bị, làm lợi cho Nhà máy hàng tỷ đồng.
Nhà máy Cán thép Thái Nguyên được lắp đặt máy cán của tập đoàn Danieli (Italia) từ năm 2003 và đến năm 2005 bắt đầu đi vào hoạt động. Tuy nhiên, trong quá trình sản xuất, dây chuyền vẫn còn xảy ra sự cố làm ảnh hưởng đến năng suất cán. Các kỹ sư trẻ của Nhà máy đã không quản ngại khó khăn, chịu khó tìm tòi, khảo sát, nghiên cứu tìm ra giải pháp để khắc phục những khuyết điểm trong hệ thống dây chuyền đó.
Đến với Nhà máy, chúng tôi được các anh dẫn đi tham quan toàn bộ Nhà máy khi hệ thống dây chuyền cán thép đang rầm rập chạy. Nhiệt độ tỏa ra từ lò nung, những thanh thép đỏ chuyển động qua dây chuyền cộng với cái nắng chói chang của tiết trời tháng Sáu tạo nên sức nóng khá lớn. Mặc cho mồ hôi nhễ nhại, các anh say sưa giới thiệu với chúng tôi về nguyên lý, cấu tạo của các phần và mối liên hệ của chúng trong dây chuyền sản xuất cán thép. Đặc biệt là những thiết bị, hệ thống mà các anh đã dày công nghiên cứu sáng tạo ra. Những thiết bị này hiện đang được áp dụng với hiệu quả cao trong dây chuyền sản xuất của Nhà máy.
Anh Đặng Kim Dũng, kỹ sư Cơ khí chế tạo máy, tác giả của đề tài “Tính toán thiết kế trạm bơm mỡ tự động cho hệ thống máy cán” cho biết: Dây chuyền cán thép của Nhà máy gồm 14 giá cán. Mỗi một giá cán có 16 điểm, vòng bi cần được bôi trơn (trong 1 giờ). Theo thiết kế thì hệ thống bơm mỡ tự động sẽ đảm nhiệm công việc này. Nhưng trên thực tế, hệ thống này không hoạt động. Việc bổ sung lượng mỡ bôi trơn thủ công không thể đáp ứng được yêu cầu vì điểm cần được bổ sung thường xuyên là quá lớn (224 điểm). Do đó, mỗi năm đã xảy ra 20 sự cố hỏng vòng bi trục cán và vòng bi gối đỡ trục chuyền vì không đảm bảo mỡ bôi trơn, gây thiệt hại hàng tỷ đồng/năm”. Sau khi tiến hành nghiên cứu khảo sát thực tế, dựa trên cơ sở của hệ thống cũ, tôi đã tính toán thiết kế trạm bơm mỡ tự động phù hợp với điều kiện sản xuất như: lắp đặt, thiết kế lại đường dây dẫn mỡ, làm thêm một nguồn mỡ và công tắc báo hiệu về trung tâm điều khiển, lắp thêm hệ thống van khóa ở mỗi trục cán để dễ dàng phát hiện và xử lý nếu xảy ra sự cố…”.
Nếu như trước khi trạm bơm mỡ tự động chưa đi vào hoạt động thì mỗi năm Nhà máy phải mất trên 3,4 tỷ đồng chi phí cho việc tiêu hao mỡ và dầu. Nhưng từ khi trạm đi vào hoạt động (từ tháng 9-2009) chi phí ấy đã giảm xuống còn trên 2,1 tỷ đồng/năm. Như vậy giá trị làm lợi từ sáng tạo này là trên 1,3 tỷ đồng/năm, chưa tính thời gian (mỗi năm lên tới 60 giờ) dây chuyền phải ngừng hoạt động để tiến hành thay thế, sửa chữa vòng bi bị hỏng như trước đây. Với đề tài sáng kiến khoa học này, anh Đặng Kim Dũng đã đạt giải Nhì của Giải thưởng Sáng tạo trẻ tỉnh lần thứ 8 năm 2010.
Còn anh Nguyễn Việt Cường (Phòng Cơ điện) với đề tài “Tính toán thiết kế chế tạo thiết bị làm mát dầu máy nén khí Compair L260” (đề tài đạt giải Ba) được áp dụng thành công đã tiết kiệm cho Nhà máy trên 900 triệu đồng. Anh nói: “Tháng 7-2010, thiết bị làm mát khí nén của dây chuyền cán thép xảy ra hiện tượng quá nhiệt, máy đã tự động dừng. Trong thời gian gần 2 tháng, Nhà máy đã phải dừng sản xuất 16 lần để khắc phục sự cố, mỗi lần khắc phục mất 4 tiếng, sản lượng giảm trên 5.000 tấn. Nhà máy đã liên hệ với các đơn vị bên ngoài có chuyên môn và kinh nghiệm để hỗ trợ khắc phục, nhưng không thành công. Kỹ sư Nguyễn Việt Cường đã tìm tòi, nghiên cứu, tính toán thiết kế và chế tạo bộ giải nhiệt dầu máy nén khí bằng nước với chi phí 12 triệu đồng. Đến cuối tháng 8-2010, thiết bị đã được đưa vào sử dụng giúp hệ thống hoạt động ổn định, việc bảo dưỡng, sửa chữa cũng dễ dàng hơn.
Cũng như hai đồng nghiệp của mình, anh Trần Đức Mạnh (phòng Kỹ thuật Công nghệ) đã có sáng tạo giúp Nhà máy đa dạng hóa được nguồn nguyên liệu đầu vào. Anh cho biết: “Theo thiết kế ban đầu, dây chuyền cán chỉ nhận phôi thép có kích thước 120x120mm và 130x130mm (kích thước vuông của phôi thép). Tuy nhiên, loại phôi có kích thước này ở thị trường trong nước và trên thế giới rất khan hiếm, giá lại cao, trong khi đó phôi thép có kích thước 150x150mm lại luôn có sẵn. Do vậy, anh đã thực hiện đề tài “Tính toán thiết kế hệ thống lỗ hình cán sản phẩm D10 (sản phẩm thép sau cán) bằng phôi 150x150mm trên dây chuyền công nghệ cán bằng phôi 130x130mm”. Kết quả, từ tháng 6-2010 đến 3-2011, Nhà máy đã sản xuất được trên 21.347 tấn sản phẩm bằng phôi 150x150mm, tiết kiệm gần 763 triệu đồng. Đề tài của anh Mạnh đã đạt giải Ba Giải thưởng sáng tạo trẻ tỉnh lần thứ 8. Được biết, anh Mạnh đã từng nhận được giải Nhất Giải thưởng Sáng tạo trẻ lần thứ 7 với đề tài “Giảm tải thiết bị hệ thống block”; giải thưởng của Liên Đoàn Lao động tỉnh với đề tài “Thiết kế hệ thống lỗ hình dùng chung cho mọi sản phẩm thép cán” năm 2010.
Ông Đoàn Đình Cự, Giám đốc Nhà máy Cán thép Thái Nguyên cho biết: Nhà máy luôn tin tưởng tạo điều kiện cho các công nhân, kỹ sư để họ có thể phát huy hết khả năng sáng tạo của mình. Nhà máy cũng chính là môi trường để họ phấn đấu, rèn luyện. Những sáng tạo của họ góp phần không nhỏ vào việc nâng cao năng suất, sản lượng, thực hiện thắng lợi nhiệm vụ sản xuất kinh doanh của Nhà máy. Năm 2010, Nhà máy đã sản xuất được 326.400 tấn sản phẩm, lần đầu tiên vượt công suất thiết kế 26.400 tấn và vượt kế hoạch của Công ty giao.